A degree of precision in every aspect of the economy impossible before the IoT is one of my fav memes, in part because it should encourage companies that have held back from IoT strategies to get involved now (because they can realize immediate benefits in lower operating costs, greater efficiency, etc.), and because it brings with it so many ancillary benefits, such as reduced environmental impacts (remember: waste creation = inefficiency!).
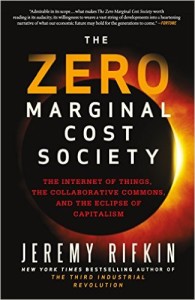
Zero Marginal Cost Society
I’m reminded of that while reading Jeremy Rifkin’s fascinating Zero Marginal Cost Economy which I got months ago for research in writing my own book proposal and didn’t get around to until recently. I’d always heard he was something of an eccentric, but, IMHO, this one’s brilliant. Rifkin’s thesis is that:
“The coming together of the Communications Internet with the fledgling Energy Internet and Logistics Internet in a seamless twenty-first-century intelligent infrastructure, “the Internet of Things (IoT),” is giving rise to a Third Industrial Revolution. The Internet of Things is already boosting productivity to the point where the marginal cost of producing many goods and services is nearly zero, making them practically free.”
Tip: when the marginal cost of producing things is nearly zero, you’re gonna need a new business model, so get this book!
At any rate, one of the three revolutions he mentioned was the “Logistics Internet.”
I’m a nut about logistics, especially as it relates to supply chain and distribution networks, which I see as crucial to the radically new “circular enterprise” rotating around a real-time IoT data hub. Just think how efficient your company could be if your suppliers — miles away rather than on the other side of the world, knew instantly via M2M data sharing, what you needed and when, and delivered it at precisely the right time, or if the SAP prototype vending machine notified the dispatcher, again on a M2M basis, so that delivery trucks were automatically re-routed to machine that was most likely to run out first!
I wasn’t quite sure what Rifkin meant about a Logistics Internet until I read his reference to the work of Benoit Montreuil, “Coca-Cola Material Handling & Distribution Chair and Professor” at Georgia Tech, who, as Rifkin puts it, closes the loop nicely in terms of imagery:
“.. just as the digital world took up the superhighway metaphor, now the logistics industry ought to take up the open-architecture metaphor of distributed Internet communication to remodel global logistics.”
Montreuil elaborates on the analogy (and, incidentally, places this in the context of global sustainability, saying that the current logistics paradigm is unsustainable), and paraphrases my fav Einstein saying:
“The global logistics sustainability grand challenge cannot be addressed through the same lenses that created the situation. The current logististics paradigm must be replaced by a new paradigm enabling outside-the-box paradigm enabling meta-systemic creative thinking.”
wooo: meta-systemic creative thinking! Count me in!
Montreuil’s answer is a “physical Internet” for logistics, which he says is a necessity not only because of the environmental impacts of the current, inefficient system (such as 14% of all greenhouse gas emissions in France), but also its ridiculous costs, accounting for 10% of the US GDP according to a 2009 Department of Transportation report! That kind of waste brings out my inner Scotsman!
Rifkin cites a variety of examples of the current system’s inefficiency based on Montreuil’s research:
- trucks in the US are, on average, only 60% full, and globally the efficiency is only 10%!
- in the US, they were empty 20% of miles driven
- US business inventories were $1.6 trillion as of March, 2013 — so much for “just-in-time.”
- time-sensitive products such as food, clothes and medical supplies are unsold because they can’t be delivered on time.
Montreuil’s “physical Internet” has striking parallels to the electronic one:
- cargo (like packets) must be packaged in standardized module containers
- like the internet, the cargo must be structured independently of the equipment, so it can be processed seamlessly through a wide range of networks, with smart tags and sensors for identification and sorting (one of the first examples of the IoT I wrote about was FedEx’s great SenseAware containers for high-value cargo!)
With the Logistics Internet, we’d move from the old point-to-point and hub-and-spoke systems to ones that are “distributed, multi-segment, intermodal.” A single, exhausted, over-worked (and more accident-prone) driver would be replaced by several. It’s a little counter-intuitive, but Montreuil says that while it would take a driver 240 hours to get from Quebec to LA under the current system, instead 17 drivers in a distributed one would each drive about 3 hours, and the cargo would get there in only 60 hours.
Under the new system, the current fractionated, isolated warehouse and distribution mess would be replaced by a fully-integrated one involving all of the 535,000 facilities nationwide, cutting time and dramatically reducing environmental impacts and fuel consumption.
Most important for companies, and looping back to my precision meme, “Montreuil points out that an open supply network allows firms to reduce their lead time to near zero if their stock is distributed among some of the hundreds of distribution centers that are located near their final buyer market.” And, was we have more 3-D printing, the product might actually be printed out near the destination. How cool is that?
Trucking is such an emblematic aspect of the 20th-century economy, yet, as with the neat things that Union Pacific and other lines are doing with the 19th-century’s emblematic railroads, they can be transformed into a key part of the 21-st century “precision economy” (but only if we couple IoT technology with “IoT thinking.”
Now let’s pick up our iPads & head to the loading dock!
PS: I’ll be addressing this subject in one of my two speeches at the SCM2016 Conference later this month. Hope to see you there!
FedEx package…