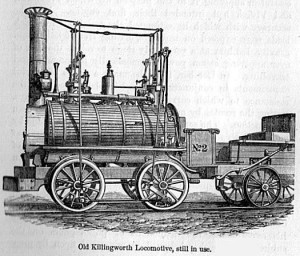
George Stephenson’s Killingworth locomotive
Source: Project Gutenberg
As those of you who know rail history understand, with Stephenson as your last name, you’re bound to have a strong interest in railroads! Add in the fact that I was associate producer of an award-winning documentary on the subject back in the early 70’s, and it’s no wonder I was hooked when I got a chance to meet with some of Siemens’s top rail executives on my trip to Barcelona last week (Disclaimer: Siemens paid my expenses, but didn’t dictate what I covered, nor did they have editorial review of this piece).
What really excites me about railroads and the IoT is that they neatly encapsulate the dramatic transformation from the traditional industrial economy to the IoT: on one hand, the railroad was perhaps THE most critical invention making possible 19th century industry, and yet it still exists, in recognizable but radically-evolved form, in 2016. As you’ll see below, trains have essentially become laboratories on wheels!
I dwelt on the example of the Union Pacific in my e-book introduction to the IoT, SmartStuff, because to CIO Lynden Tennison was an early adopter, with his efforts focused largely on reducing the number of costly and dangerous derailments, through measures such as putting infrared sensors every twenty miles along the rail bed to spot “hotboxes,” overheating bearings. That allowed an early version of what we now know as predictive maintenance, pulling cars off at the next convenient yard so the bearings could be replaced before a serious problem. Even though the technology even five years ago was primitive compared to today, the UP cut bearing-related derailments by 75%.
Fast-forward to 2016, and Siemens’s application of the IoT to trains through its Mobility Services is yielding amazing benefits: increasing reliability, cutting costs, and even leading to possible new business models. They’ve taken over maintenance for more than 50 rail and transit programs.
While I love IoT startups with a radical new vision and no history to encumber them, Siemens is a beacon to those companies firmly rooted in manufacturing which may wonder whether to incorporate the IoT in their services and strategy. I suspect that its software products are inherently more valuable than competitors from pure-play software firms at commercial launch because the company eats its own dogfood and applies the new technology first to the products it manufactures and maintains — closing the loop.
Several of its executives emphasized that one of the advantages Siemens feels they enjoy is that their software engineers in Munich work in a corner of an old locomotive factory that Siemens still operates, so they can interact with those actually building and maintaining the engines on a daily basis. When it comes to security issues, their experience as a manufacturer means they understand the role of each component of the signaling system. Dr. Sebastian Schoning, ceo of Siemens client Gehring Technologies, which manufactures precision honing tools, told me that it was easier to sell these digital services to its own client base because so much of their current products include Siemens devices, giving them confidence in the new offerings. GE enjoys the same advantages of combining manufacturing and digital services with its Evolution Series locomotives.
The key to Siemens’s Mobility Services is Sinalytics, its platform architecture for data analysis not just for rail, but also for industries ranging from medical equipment to wind farms. More than 300,000 devices currently feed real-time data to the platform, Consistent with my IoT-centric “Circular Company” vision, Sinalytics capitalizes on the data for multiple uses, including connectivity, data integration, analytics, and the all-important cyber security — they call the result not Big Data, but Smart Data. As with data services from jet turbine manufacturers such as Rolls Royce and GE, the platform also allows merging the data with data from sources such as weather forecasts which, in combination, can let clients optimize operating efficiency on a real-time M2M basis.
With the new approach, trains become IoT laboratories on wheels, combining all of the key elements of an IoT system:
- Sensing: there are sensors on the engines and gearboxes, plus vibration sensors on microphones measure noises from bearings in commuter trains. They can even measure how engine oil is aging, so it can be changed when really needed, rather than on an arbitrary schedule.
- Algorithms to make sense of the data and act on it. They read out patterns, record deviations & compare them with train control systems or vehicles of the same type.
- Predictive maintenance replaces scheduled maintenance, dramatically reducing down-time and catastrophic failure.For example: “There’s a warning in one of the windows (of the control center display): engine temperature unusual. ‘We need to analyze the situation in greater depth to know what to do next — we call it ‘root cause analysis,” (say) Vice-President for Customer Support Herbert Padinger. ‘We look at its history and draw on comparative data from the fleet as a whole.’ Clicking on the message opens a chart showing changes in temperature during the past three months. The increased heat is gradually traced to a signal assembly. The Siemens experts talk with the customer to establish how urgent the need for action is, and then takes the most appropriate steps.” He says that temperature and vibration analyses from the critical gearboxes gives Siemens at least three days advance notice of a breakdown — plenty of time for maintenance or replacement. Predictive maintenance is now the norm for 70-80% of Siemens’s repairs.
- Security (especially important given all of the miles of track and large crowds on station platforms): it includes video-based train-dispatch and platform surveillance using its SITRAIL D system, as well as cameras in the trains. The protections have to run the gamut from physical attacks to cyber attacks. For security, the data is shared by digital radio, not networks also shared by consumers.
When operations are digitized, it allows seamlessly integrating emerging digital technologies into the services. Siemens Digital Services also included augmented reality (so repair personnel can see manuals on heads-up displays), social collaboration platforms, and — perhaps most important — 3-D printing-based additive manufacturing, so that replacement parts can be delivered with unprecedented speed. 3-D printing also allows dramatic reduction in parts inventories and allows replacement of obsolete parts that may no longer be available through conventional parts depots or even — get this — to improve on the original part’s function and/or durability, based on practical experience gained from observing the parts in use. Siemens has used 3-D printing for the past last 3 years, and it lets them assure that they will have replacements for the locomotive’s entire lifespan, which can exceed 30 years.
The results of the new approach are dramatic.
- None of the Velaro trains that Siemens maintains for several operators have broken down since Sinalytics was implemented. Among those in Spain only 1 has left more than 15 min. behind time in 2,300 trips: .0004%!
-
Reliability for London’s West Coast Mainline is 99.7%
-
Perhaps most impressive, because of the extreme cold conditions it must endure, the reliability rate for the Velaro service in Russia is 99.9%!
Their ultimate goal is a little higher: what Siemens calls (pardon the pun) 100% Railability (TM).
And, consistent with what other companies find when they fully implement not only IoT technology, but also what I like to call “IoT Thinking,” when it does reach those previously inconceivable quality benchmarks, the company predicts that, as the software and sensors evolve, the next stage will be new business models in which billing will be determined by guaranteeing customers availability and performance.
PS: I’ll be posting more about my interviews with Siemens officials and the Gartner event in coming days.